Engenharia e Inspeção de Soldagem MAG em Aços Inoxidáveis: Tudo o que Você Precisa Saber
- ACW Group
- 30 de jan.
- 4 min de leitura
A soldagem de aços inoxidáveis é um processo crítico para diversas indústrias, como farmacêutica, alimentícia e química, especialmente na fabricação de tanques de aço inox, reatores e equipamentos de bioprocessamento. Entre os métodos mais utilizados, destaca-se o processo MIG/MAG, que combina eficiência, produtividade e qualidade da junta soldada.
Neste artigo, exploramos a influência da engenharia de soldagem MAG em chapas espessas de aço inoxidável AISI 316L, comparando diferentes modos de transferência metálica: curto-circuito, spray e pulsado. Além disso, avaliamos o impacto da soldagem na resistência à corrosão e na microestrutura da junta soldada.
O Que é a Soldagem MAG e Por Que é Importante para o Aço Inoxidável?
A soldagem MAG (Metal Active Gas) é amplamente utilizada para unir componentes metálicos de forma eficiente e resistente. No caso do aço inoxidável AISI 316L, a escolha correta do modo de transferência de metal na soldagem pode impactar diretamente na resistência à corrosão, na formação da microestrutura e na qualidade final da junta soldada.
Principais desafios na soldagem MAG do aço inoxidável:
✅ Controle do aporte térmico, essencial para evitar deformações e alterações microestruturais.
✅ Minimização da precipitação de fase sigma, uma fase deletéria que reduz a resistência à corrosão.
✅ Garantia de uma boa propriedade de passivação, fundamental para aumentar a durabilidade da solda.
Comparação dos Modos de Transferência Metálica na Soldagem MAG
O estudo analisou a soldagem MAG de chapas espessas (5/8”) do aço inoxidável AISI 316L, comparando três modos de transferência metálica e seus impactos na microestrutura e resistência à corrosão:
1) Modo Pulsado: Baixo aporte térmico (0.7 kJ/mm), menor aquecimento da junta, microestrutura mais homogênea e ausência de fase sigma.
2) Modo Curto-Circuito: Aporte térmico intermediário (1.2 kJ/mm), com formação de fase sigma no interior da ferrita-delta.
3) Modo Spray: Maior aporte térmico (1.9 kJ/mm), resultando em grãos grosseiros, alto teor de ferrita-delta e fase sigma nos contornos da ferrita-delta.
A Figura 1 ilustra a seção transversal das juntas soldadas.

O controle do aporte térmico foi um fator determinante na formação da microestrutura da solda. Na Figura 2, podemos ver a estrutura bifásica típica do aço inoxidável AISI 316L, composta por ferrita-delta e austenita com morfologia dendrítica.

Impacto da Soldagem na Formação da Fase Sigma e na Corrosão
A fase sigma é um composto rico em cromo e molibdênio, prejudicial para a resistência à corrosão do aço inoxidável. A análise revelou que:
1) Modo spray: fase sigma precipitou nos contornos da ferrita-delta.
2) Modo curto-circuito: fase sigma precipitou no interior da ferrita-delta.
3) Modo pulsado: não apresentou precipitação de fase sigma.
A formação dessa fase foi analisada por microscopia eletrônica de varredura (MEV) no modo BSE, destacando-se em branco na Figura 3.
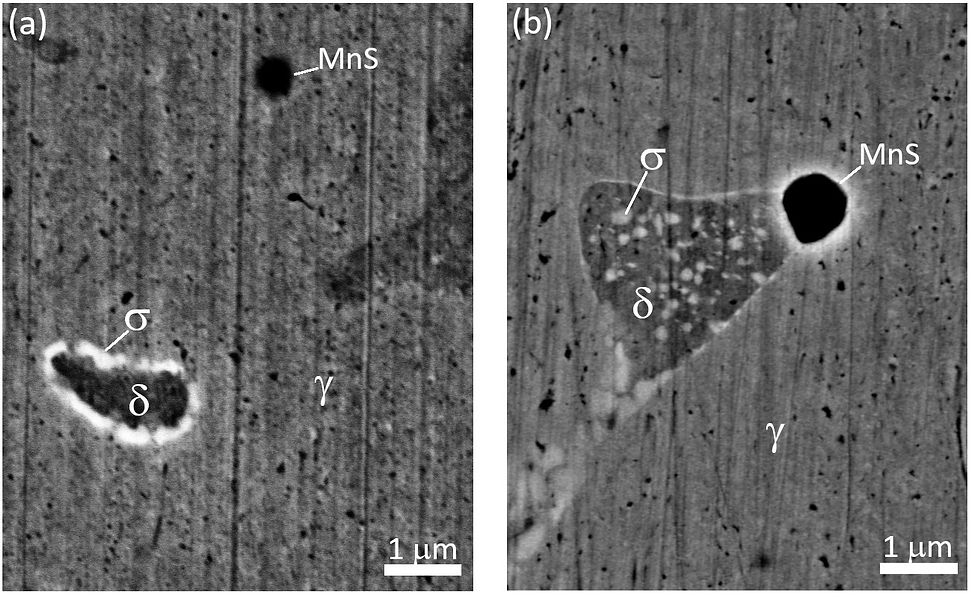
A resistência à corrosão das juntas soldadas foi avaliada por polarização potenciodinâmica cíclica (CPP). Os resultados indicaram que:
✅ O modo pulsado apresentou a melhor resistência à corrosão, pois não gerou fase sigma.
✅ O modo spray teve a maior corrosão localizada, devido à formação de fase sigma nos contornos de ferrita-delta.
✅ O modo curto-circuito demonstrou corrosão preferencial da ferrita-delta, comprometendo a integridade da junta soldada.

Corrosão Preferencial em Função do Modo de Transferência
A microanálise química revelou que a fase sigma cria um efeito galvânico, acelerando a corrosão da junta soldada. Os resultados mostraram que:
🔹 Modo spray: austenita foi a fase mais corroída.
🔹 Modo curto-circuito: ferrita-delta foi a fase mais corroída.
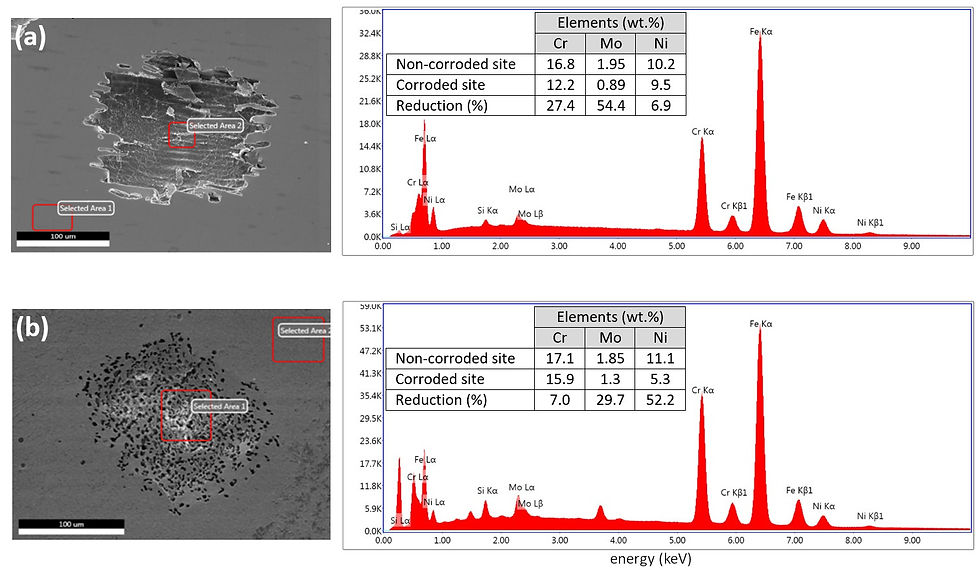
Ensaios eletroquímicos adicionais confirmaram que a posição da fase sigma influencia diretamente a corrosão preferencial:

Conclusões: Qual o Melhor Processo de Soldagem para o Aço Inoxidável 316L?
Com base nos resultados obtidos, as principais conclusões são:
✔️ A soldagem MAG no modo pulsado é a melhor opção para chapas espessas de aço inox 316L, pois garante maior resistência à corrosão e melhor propriedade de passivação.
✔️ A precipitação de fase sigma reduz significativamente a resistência à corrosão, tornando os modos curto-circuito e spray menos recomendados para aplicações de alta exigência.
✔️ A face da solda é a região mais resistente à corrosão, devendo ser exposta ao meio corrosivo em aplicações industriais.
Se você busca soluções especializadas em soldagem, eletropolimento e passivação de aços inoxidáveis, entre em contato com a ACW Engenharia e conte com a expertise de quem entende do assunto!
📞 Fale Conosco: https://wa.me/551630142240 ou (16) 3014-2240
Comentários